Meeting & Venue Details
All times listed are central.
Hybrid Event
The event will be both in-person and virtual/online. The in-person venue is Transocean in Houston. Please register early to ensure your seat.
When arriving at Transocean, ensure you allow extra time to pass through building security. There will be a separate table when you walk into the building with Transocean security badges for each pre-registered attendee. Participants must show a government photo ID to receive their security badge. Transocean Offshore Training Facility, Second Floor Meeting Room. *Please park above the second floor of the parking garage.
IADC ART Spark Tank
To encourage innovation in the drilling industry, IADC ART is restarting our Spark Tank event series after a short hiatus. Spark Tank is a forum to “spark” new thinking. It is an opportunity to provide active and aspiring technology entrepreneurs with a new opportunity to pitch their products and ideas to a panel of drilling contractors, operators and service companies (“sharks”).
The purpose is to provide insights (“sparks”) to technology developers into what matters to those they are innovating for. There is sometimes a vast disconnect between a good idea and a great product, and these events attempt to close that gap in a good-natured, productive manner. Spark Tank presentations will allow the Sharks to ask questions and provide technical and business feedback from the perspective of the product’s intended end user.
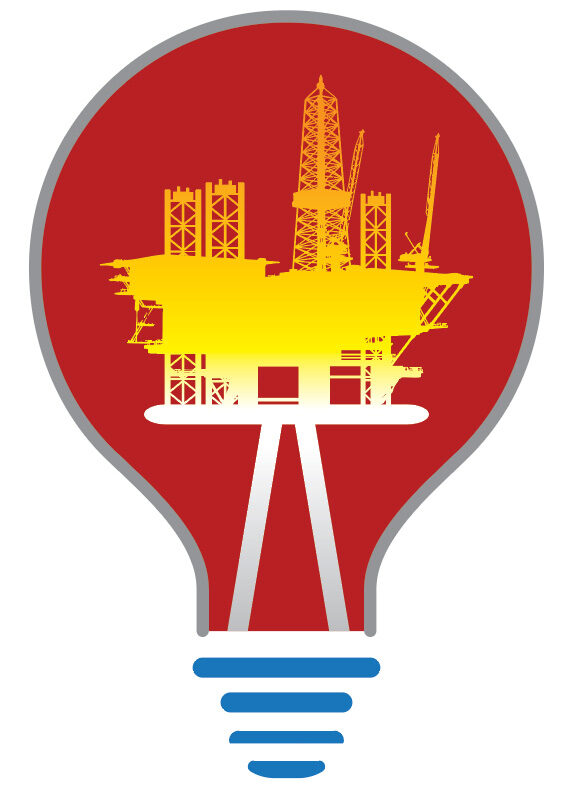
Thanks to our Drilling Sharks:
- Paul Sullivan, Innovation Portfolio Manager, Noble
- Matt Rayson, Product Director, Caterpillar Oil & Gas
- Jeff Walker, Automation Specialist, BP
- Trent Martin, Transocean, and Alex Groh, Patterson-UTI (ART Co-Chairs and moderators)
Agenda
8:30 Coffee and networking
9:00 Welcome, introductions and facility safety briefing – Robin Macmillan, former IADC ART Chair
Speakers have 15 minutes, with 15 minutes allotted for Sharks’ Q&A:
9:15 “Size AND Shape Matter: How Can We Accelerate the Industry’s Integration of New Data?”: Calvin Holt, DrillDocs
The modern drilling rig is widely instrumented and monitored – except for the shale shakers. Despite being the best place to directly observe what is being drilled and how much of it is being successfully removed from the wellbore, intermittent “bucket tests” are still widely accepted as a best practice for cuttings measurement and cavings detection.
Cuttings recovery rate is an essential measure of how effectively the borehole is being cleaned, with inadequate hole cleaning leading to overpulls, increased torque, and stuck pipe responsible for millions of dollars of NPT and lost equipment. Cavings are a warning sign of borehole instability, with prompt remedial action needed to avoid borehole enlargement or borehole collapse, which can once again lead to stuck pipe.
In this presentation we will show how camera-as-a-sensor technology and AI-enabled image analysis are dramatically improving the quality and quantity of information being gathered at the shale shaker. Images captured at the exit of each shale shaker are interpreted to identify cuttings and cavings, quantify their size and shape, and provide valuable inputs to drilling-related simulations and on-site decision making.
The availability of real-time cuttings size and shape data will also be a key input to reliable drilling automation and eventually to autonomous drilling. The question is: How long will it take for the drilling community to accept and integrate the results of digital shaker surveillance?
9:45 “AI-Enabled Digital Drill Bit Forensics – It’s Available Now”: Sean Emery, Trax Electronics
IADC dull bit grading is the current industry standard to document the condition of a dull drill bit. However, since today’s methods rely on human interaction and judgement, the resulting data is severely limited in terms of its accuracy, its consistency, and its comparability. As a result, the usefulness of this data in improving how bits are designed and operated is also severely limited.
This presentation will give an overview of new technology that has been developed to:
i) scan dull drill bits and build very high-resolution 3D models of these bits that can be viewed by anyone, any time, anywhere in the world,
ii) use artificial intelligence to perform assessments of the wear and damage on each of the individual cutters as well as the body of the bit,
iii) enable access to very-high-resolution photos of every cutter from different perspectives
iii) provide analytics capabilities that enable wear and damage pattern recognition, and allow correlation with drilling data to identify drilling dysfunctions; and
iv) facilitate collaboration between E&P and service provider stakeholders working toward optimized drilling operations
The presentation will provide an overview of the technology, along with actual examples of dull bit scans, cutter wear and damage analyses, high resolution cutter photos, and correlations with EDR data.
10:15 Networking Break
10:30 “Using 3D Printing to Innovate the Hydraulic Performance of PDC Bits”: Justin Jones, Texas A&M University student
PDC bits are central to deep drilling, with current designs already improving the ROP in challenging formations. We propose to enhance ROP through innovative hydraulic designs enabled by 3D metal printing. Innovations focus on increasing fluid velocities, altering flow geometry to create low-pressure zones, or inducing cavitation around cutters, to reduce hydrostatic forces that resist rock removal. By lessening these forces and minimizing rock ribbon formation, energy normally used to overcome resistance is redirected to scrape rock, lowering the MSE needed to drill a formation.
Prototype bits have been 3D printed in plastic or stainless steel and tested via a laboratory scale drilling rig to verify hydraulic performance and calibrate the fluid model. The tests yielded promising results, indicating that this approach of lowering fluid pressures around the cutter faces may lead to significant improvements in drilling efficiency and reductions in operational costs. These findings support further research and development in PDC bit innovation, potentially offering substantial benefits to the deep drilling industry.
11:00 “AI-powered Documentation and Knowledge Management”: Charlie Cubitt, KnowledgeBox Solutions
Drilling operations continue to lose millions of dollars to Non-Productive Time, Lost-Time Incidents, and well-control events—failures often rooted in fragmented documentation, knowledge gaps, and communication barriers. This underscores the need for a smarter, always-accessible knowledge management system. An AI-powered platform can embed specialist “co-pilots” in every department. Crews can “talk” to their manuals, generate safety materials on demand, analyze data and generate reports, turn raw notes into intelligence, bridge communication gaps, and seek expert guidance for every task.
11:30 Adjournment
For more information, contact Linda Hsieh, linda.hsieh@iadc.org, +1-713-292-1945, ext 219.
IADC ART Committee Mission
To improve safety and efficiency through sound operating procedures, design of automated systems and standardizing automation.